Perform molds are essential components of the plastic bottle manufacturing process. They are used to produce the initial shape of a plastic bottle, which is then stretched and blown to the final desired size and shape. Preform molds are typically made from high-quality steel and designed to withstand the high pressure and temperature required for the molding process. In this article, we will discuss the different types of perform molds, their design considerations, and their applications in the plastic bottle manufacturing industry.
Types of Preform Molds
There are two main types of performed molds: injection and blow molds. Injection molds are used to produce the initial preform shape, which is then transferred to a blow mold where it is stretched and blown to the final shape. Injection molds can produce a high volume of preforms at a fast rate, making them ideal for large-scale production. On the other hand, blow molds are used for lower volume production and can produce a wider range of bottle shapes and sizes.
Design Considerations
When designing perform molds, several factors must be considered. One of the most important factors is the type of plastic material being used. Different plastic resins have varying flow rates and cooling characteristics, which can affect the design of the mold. Other factors to consider include the size and shape of the preform, the number of cavities in the mold, and the temperature and pressure required for the molding process.
Applications
Perform molds are used in a wide range of applications, including the production of water bottles, juice bottles, and other food and beverage containers. They are also used in the production of cosmetic and personal care products, such as shampoo bottles and lotion containers. The ability to produce preforms in a variety of shapes and sizes makes them a versatile solution for many different industries.
Conclusion
Preform molds play a critical role in the plastic bottle manufacturing process. They are used to produce the initial shape of the bottle, which is then stretched and blown to the final shape. There are two main types of performed molds, injection, and blow molds, each with its own advantages and limitations. When designing preform molds, several factors must be considered, including the type of plastic material being used, the size and shape of the preform, and the temperature and pressure required for the molding process. With their versatility and efficiency, perform molds are an essential component of many different industries.
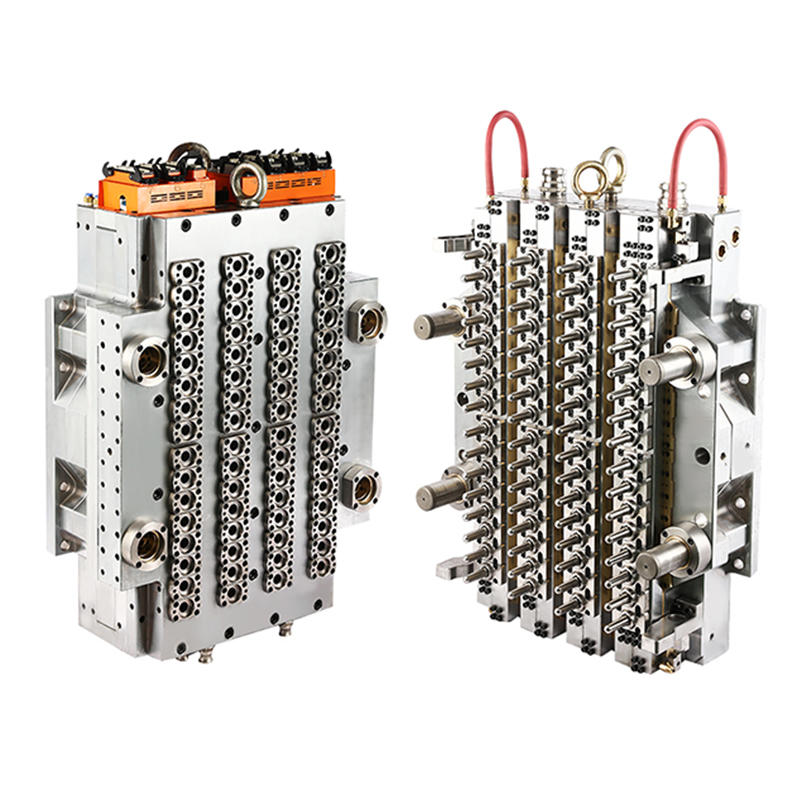
64 Cavity PET Preform Mould
Product Name | 64 Cavity PET Preform mould |
Core &Cavity Steel | S136,FS636,632 (Chinese Steel) ASSAB S136(Sweden) |
Mould base | P20,4Cr13, Standard Mould Base |
Steel hardness: | HRC32-35 for slider and stripper palte and other plates |
HRC49-51 for core and cavity material. | |
HRC49-51 for Neck ring and Lock ring | |
Plastic material | PET resin |
Cavity Number | 1x8, 1x16,1x24,1x32,1x48,1x64,1x72 |
Injection System | Short tail, Long tail, Pin Valve gate |
Ejector System | Stripper plate |
Cycle Time | Based on preform weight |
Delivery Time | 45-60 Days |
Mould lifetime | At least 3 million Shots |
Warranty Time | One Year or 1million shots |