Selecting the right 48-cavity PET preform mold is crucial for manufacturers engaged in high-volume production of PET preforms. The mold plays a significant role in determining the quality, efficiency, and overall success of the production process. We will explore the key factors to consider when selecting a 48-cavity PET preform mold and how they contribute to achieving optimal quality and efficiency in high-volume production.
Mold Material: The choice of mold material is critical as it affects various aspects of the production process. Commonly used materials for PET preform molds include stainless steel and aluminum alloys. Stainless steel molds offer excellent durability, thermal conductivity, and corrosion resistance, making them suitable for long production runs. Aluminum molds, on the other hand, provide faster cooling times and reduced cycle times, which can be advantageous for high-volume production. The selection of the mold material should align with the production requirements and consider factors such as production volume, cycle time, and maintenance considerations.
Mold Design: The design of the 48-cavity PET preform mold plays a crucial role in achieving optimal quality and efficiency. The mold design should incorporate features that ensure uniform cooling, consistent wall thickness, and proper ejection of preforms. A well-designed mold minimizes the risk of defects such as warpage, shrinkage, or non-uniform wall thickness, resulting in high-quality preforms. It should also consider factors such as gate design, cooling channel layout, and venting, all of which contribute to efficient and reliable production.
Cooling System: Efficient cooling is essential for the high-volume production of PET preforms. The mold should incorporate an effective cooling system to ensure rapid and uniform cooling of the preforms. This helps in achieving shorter cycle times and reducing the risk of defects caused by inadequate cooling, such as inconsistent dimensions or crystallization issues. Proper cooling also enhances the overall productivity and efficiency of the production process by allowing for faster mold opening and shorter cooling times between cycles.
Injection System: The injection system of the 48-cavity PET preform mold should be designed for precise and consistent material distribution. It should provide optimal control over the injection parameters, such as injection speed, pressure, and melt temperature, to ensure accurate preform dimensions and wall thickness. A well-designed injection system minimizes variations in perform weight, enhances dimensional stability, and contributes to efficient material usage. It is also crucial to consider features like hot runner systems or valve gate systems, which allow for precise control and minimize material waste.
Maintenance and Serviceability: Considering the maintenance and serviceability aspects of the mold is vital for uninterrupted high-volume production. The mold should be designed for ease of maintenance, with features that allow for quick mold changes, easy cleaning, and accessibility to critical components. Proper maintenance practices, including regular cleaning, inspection, and lubrication, ensure the longevity and consistent performance of the mold. Additionally, selecting a reputable supplier or manufacturer who provides reliable technical support and spare parts availability is crucial for minimizing downtime and optimizing production efficiency.
Quality Assurance: In high-volume production, achieving consistent quality is of utmost importance. The mold should undergo rigorous testing and quality assurance procedures to ensure its reliability and capability to consistently produce high-quality preforms. Consideration should be given to factors such as mold validation, dimensional accuracy, and conformity to industry standards and regulations. Investing in a high-quality 48-cavity PET preform mold reduces the risk of production delays, rejects, and customer dissatisfaction, ultimately contributing to improved efficiency and profitability.
In conclusion, selecting the right 48-cavity PET preform mold is a critical decision for manufacturers engaged in high-volume production. By considering factors such as mold material, design, cooling system, injection system, maintenance, and quality assurance, manufacturers can achieve optimal quality and efficiency in their production processes. A well-designed and properly maintained mold ensures the production of high-quality preforms, reduces cycle times, minimizes defects, and enhances overall productivity.
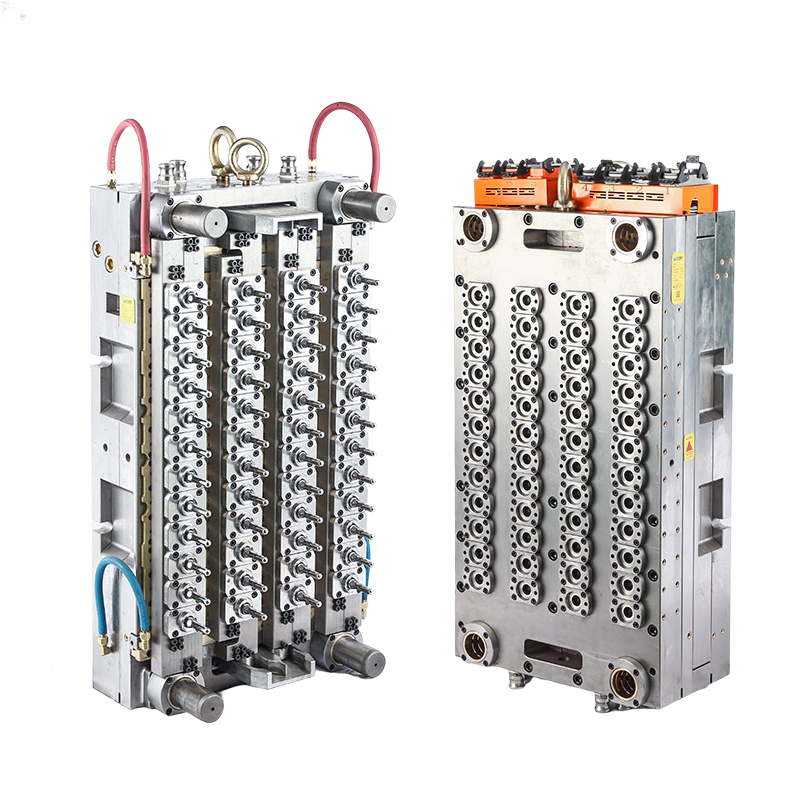
48 Cavity PET Preform Mould
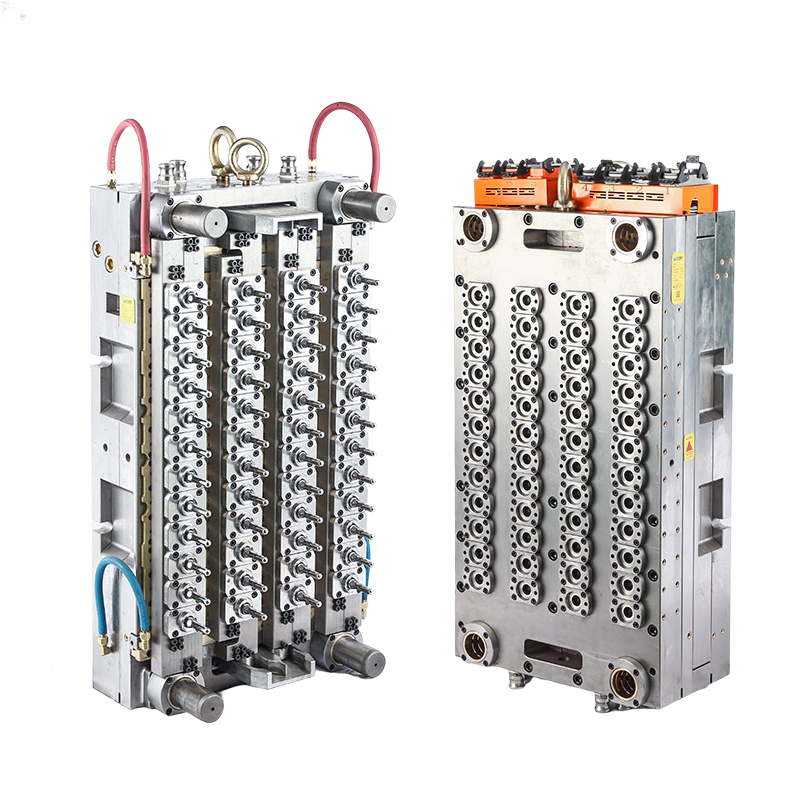
48 Cavity PET Preform Mould